【導入事例】費用や工数の削減、非稼働時間の可視化を実現した3つの事例をご紹介!
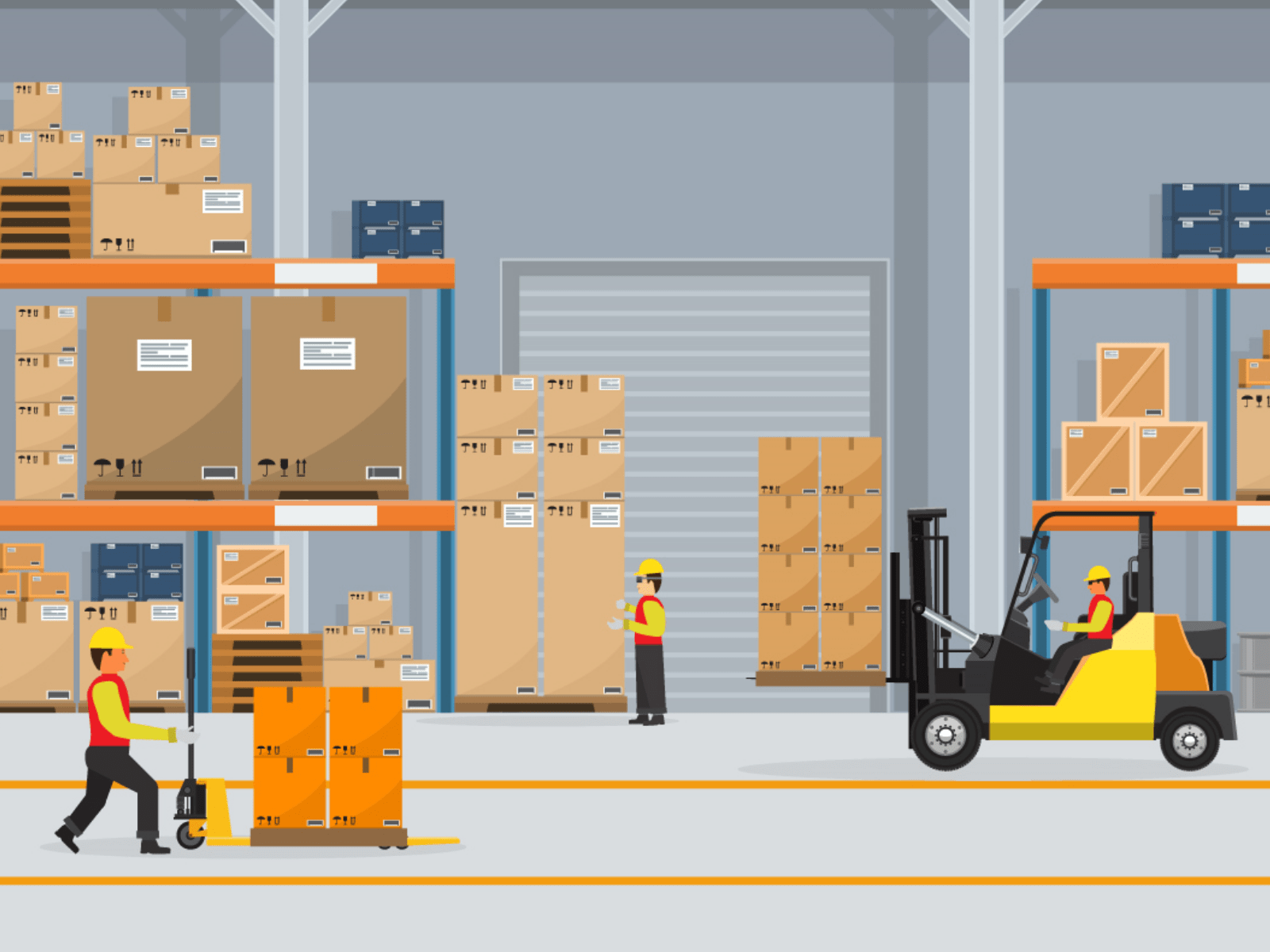
RFIDを用いて工場・倉庫の動線・滞留を可視化する「動線見える化ツール」。作業効率化やレイアウトの改善に役立てることができ、これまで、全国で50以上の工場・倉庫で導入いただいております。
この記事では、実際に導入している企業さまがどのような背景から導入に至り、どんな導入効果があったのか、3つの事例をご紹介いたします。
Case-1 フォークリフトの余剰分を割り出し、月20万円の削減に成功
導入背景/ご要望
- 子会社・関連会社を多く抱えており、管理の目が行き届いていなかった
- 倉庫内に余剰なフォークリフトがあるのではないかと考えていたが判断できる根拠がなく、データを取得する方法を探していた
- コスト削減が目的であるため、調査のツールに大規模な投資ができない
実現方法
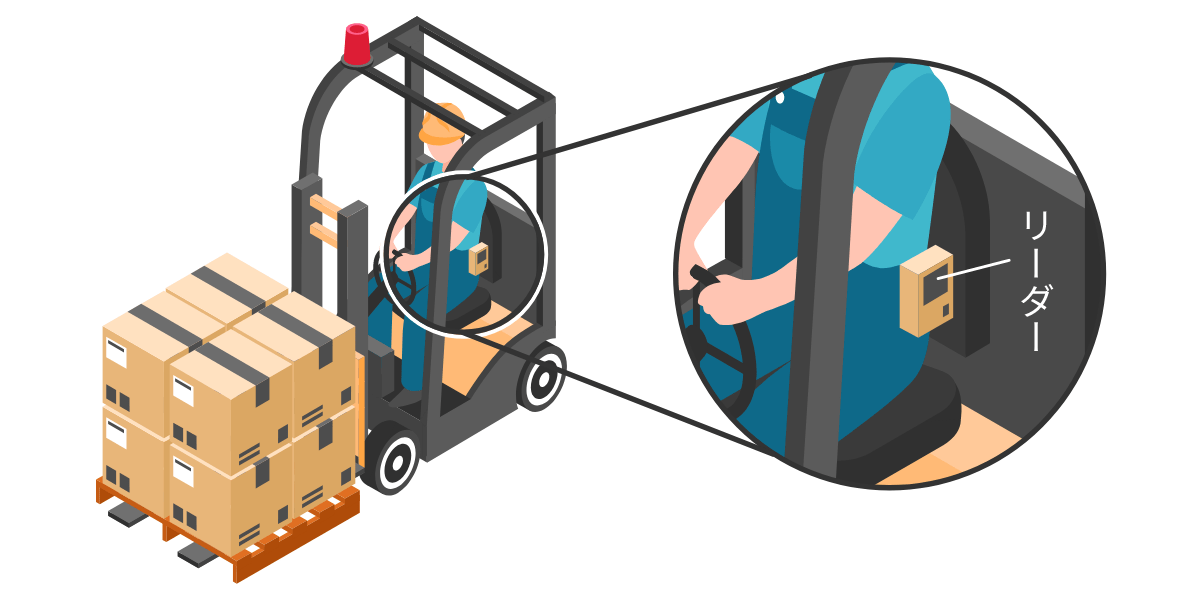
- 全てのフォークリフトにリーダーを設置し、倉庫随所にタグを配置
- 通過情報の他、滞留時間や稼働率を算出
⇒フォークリフトごとのパフォーマンスを知ることができるようにした
導入効果
測定対象倉庫において、8台のフォークリフトのうち2台が極端に稼働率が低く余剰であることが判明。リース契約を解除し、約20万円/月の削減に成功しました。他の倉庫でも余剰や不足がないか検証するため導入をすすめています。
関連製品
マーストーケンさまのUHFフォークシステムとの連携のご提案も可能です。
https://www.mars-tohken.co.jp/rfid/products/rfid-package/uhf_fork/
フォークリフトを活用した荷物のロケーション管理などをご検討の皆さま、ぜひご覧ください。
Case-2 ピッキングの移動距離を大幅削減して、約45時間/月の工数削減
導入背景/ご要望
- 深刻な人材不足により現場の負荷が増大。各作業者の負担を軽減することが急務
- 親会社からの業務改善の指示に対し、エビデンスを示しながら改善活動を進める必要があった
- 倉庫内の在庫のロケーションを変更してみたが、本当に効果的に配置できているのか判断できず、うまくPDCAを回せていなかった
実現方法
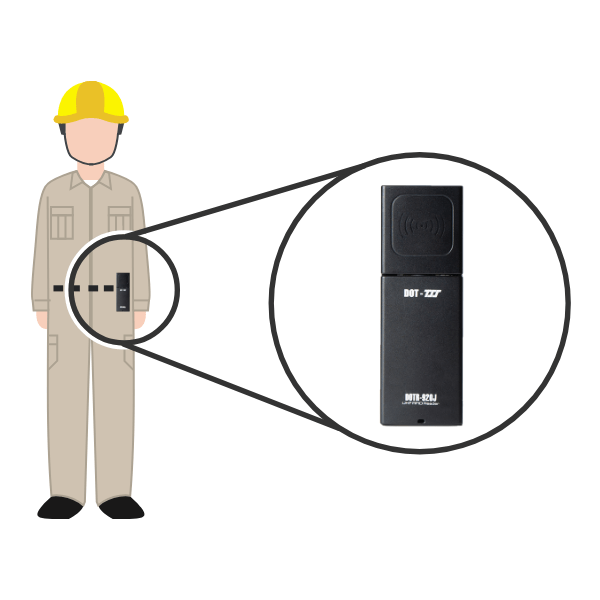
- ピッキング担当者の腰にリーダーを設置し、倉庫随所にタグを配置
- 出荷頻度上位のアイテムを配置変更しながら各作業者の移動距離を検証
⇒作業者にかかる負荷を把握しつつ、最適な在庫のレイアウトを模索した
導入効果
現場作業員の移動距離が大幅に減ったことにより、工数の削減にも成功しました。
<負荷軽減>
1ピックあたりの平均移動距離を3.8m → 2.8mに減らすことに成功。1日約3万歩だった移動距離を大幅に削減
<業務改善>
作業者の負荷軽減に伴い、約45時間/月の工数削減に成功
<安心安全>
レイアウト変更によりフォークリフトと作業者を分離できた
Case-3 業務に工夫を加えることで、作業者の非稼働時間の可視化を実現
導入背景/ご要望
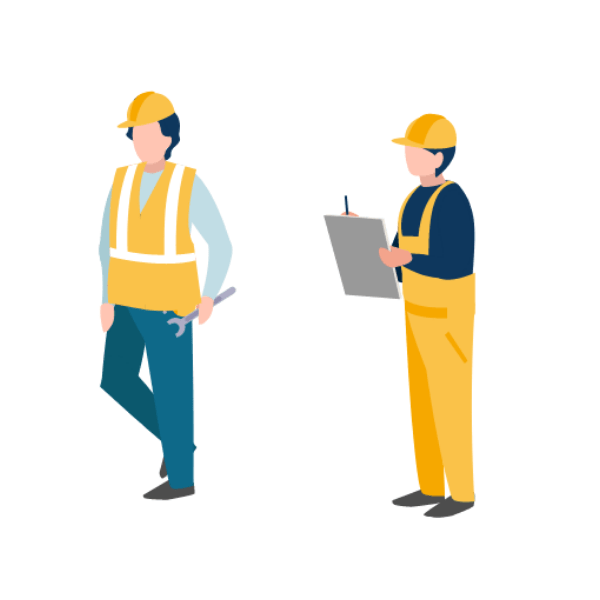
- 作業者の「手待ち時間」を可視化したい
- いつもはバインダーを持って作業者と一緒に動き、位置情報と作業内容を取っていた
実現方法
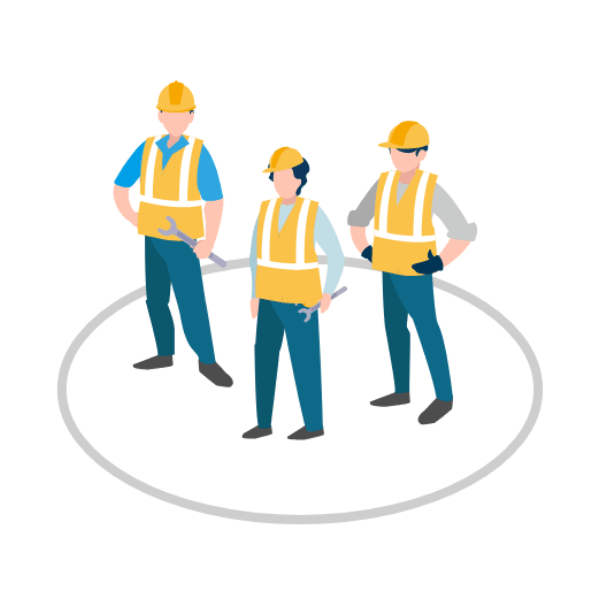
本ツールは測定対象の位置情報を取得するもののため、本来は作業しているのか手待ちなのかは判別できない。しかしながら「手待ち中はこのエリアで待機する」というルールを設けることで作業中か手待ちかの見える化を図った。
導入効果
今回の目的だった「手待ち時間の可視化」に成功。データ取りにかかる時間(およそ2週間×2人の工数)も削減でき、取得したデータの分析も楽に実施できた。
今回得たデータをもとに手待ち時間の内容を調査した結果、作業者を1人減らす計画を立てている。
まとめ
3つの事例では、動線や滞留時間などのデータを可視化することで、根拠を持って改善活動に取り組むことができ、費用や工数の削減、非稼働時間の可視化などの導入効果を上げることができたようです。
動線見える化ツールは工事不要、RFIDを設置するだけで簡単に導入することができます。測定範囲を後から広げたいときも安価なRFIDを増やすだけ、測定場所の変更も簡単です。
さらに詳しい情報をお知りになりたい方は、ぜひその他のコンテンツもご覧ください。